Unlocking the Full Potential of Synthetic Diamond Manufacturing with AI and Big Data
In the precision-driven world of synthetic diamond production, every percentage of efficiency gained translates into measurable value. This case study showcases how data and AI can redefine what’s possible in a traditional manufacturing process — transforming manual operations into a smart, self-optimising system.
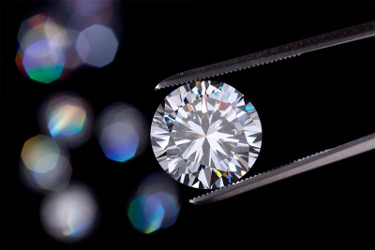
From Manual Judgement to AI-Powered Precision
Traditionally, engineers in the synthetic diamond industry relied on post-production inspection results and personal experience to adjust operational parameters for the next production cycle. This manual tuning approach varied widely among individuals and often delivered inconsistent results.
To address this, our team deployed an AI-powered intelligent tuning algorithm that aggregates expert knowledge across the organisation. The algorithm automatically determines the optimal adjustment direction and scale for the cubic press machine’s power and pressure, helping each production cycle operate at peak efficiency. The result? Significantly improved consistency and higher yields — with less manual effort.
Proof of Concept (POC): Small Test, Big Insight
Before full deployment, we conducted a Proof of Concept (POC) to validate the feasibility of this intelligent approach. Using our self-developed data platform, we quickly constructed a digital model of the cubic press, integrating historical and real-time IoT data streams — including temperature, power, pressure, current, and voltage.
During the POC, we uncovered a key insight: contrary to previous assumptions, temperature and pressure were the primary drivers of crystal quality, not cooling water temperature. This discovery led to a refined model that incorporated:
- Confidence metrics from visual inspection
- Discrepancy analysis between set and actual press parameters
- Recommendations for replacing manual inspections with AI-driven visual systems
These refinements not only increased the confidence in inspection results but also streamlined the entire analysis process.
Intelligent Algorithms Deliver High-Value Results
The final tuning solution combined neural networks, genetic algorithms, and deep learning techniques like Faster R-CNN to detect and optimise for ideal crystal formation. The algorithm dynamically adapts to each production run, ensuring that the graphite columns consistently achieve optimal shape and uniform crystal distribution. This directly translates into higher product quality, elevated pricing, and increased profitability.
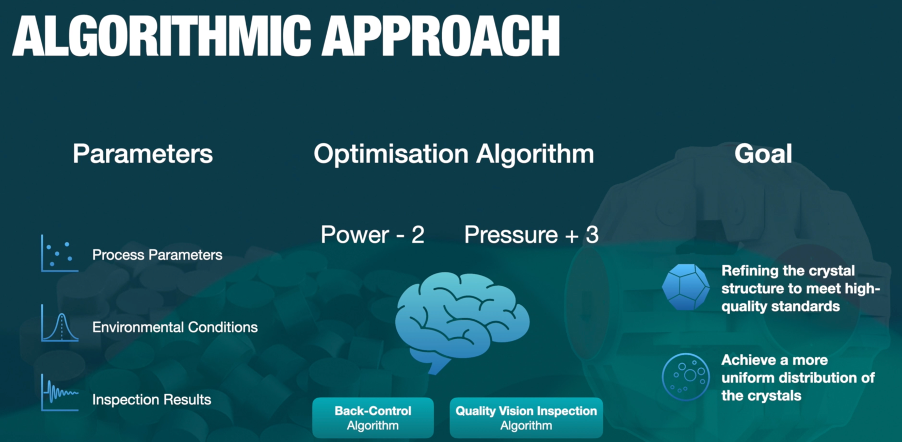
Full-Scale Implementation: Automation at Scale
With a successful POC behind us, we launched a Full-Scale Implementation (FSI) across the factory floor — covering nearly 500 cubic press machines. The system now automates PLC data acquisition, inspection result processing, and parameter tuning, eliminating the need for on-site adjustments. Engineers can now remotely manage a significantly higher number of machines, improving efficiency and reducing operational overhead.
The Platform That Powers It All: DPLUS
At the core of this transformation lies the DPLUS™ platform — an industrial AI and data intelligence solution built to empower manufacturers with end-to-end visibility and intelligent control.
DPLUS allows engineers and analysts to quickly build digital models of equipment like the cubic press machine, using both historical records and real-time IoT data inputs. From pressure and power to temperature and voltage, DPLUS ingests multi-dimensional sensor data, enabling seamless integration of AI algorithms and intuitive visualisation dashboards.
Thanks to its hardware-agnostic architecture, DPLUS supports:
- Real-time monitoring
- Predictive analytics
- Model-driven optimisation
- Seamless scaling across factory floors
In this project, DPLUS enabled fast POC validation and smooth transition into full-scale deployment — all without overhauling existing workflows. By acting as both the digital backbone and the intelligent engine, DPLUS™ turned operational data into a competitive advantage.
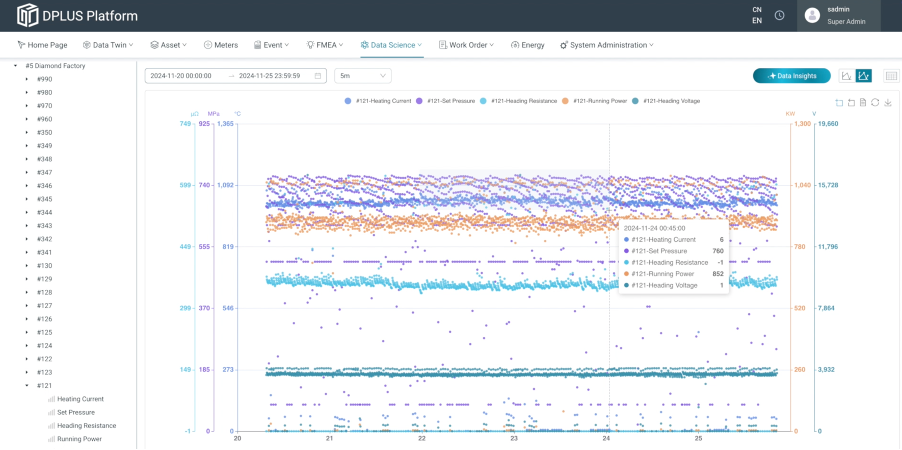
Whether applied to synthetic diamond production, steel manufacturing, or broader smart factory initiatives, DPLUS provides a flexible, scalable, and intelligent foundation for digital transformation.
💡 Want to bring intelligent optimisation to your own production line?
Talk to us today and discover how our platform can turn your operations into a smart, scalable, and data-driven success.
About the Author
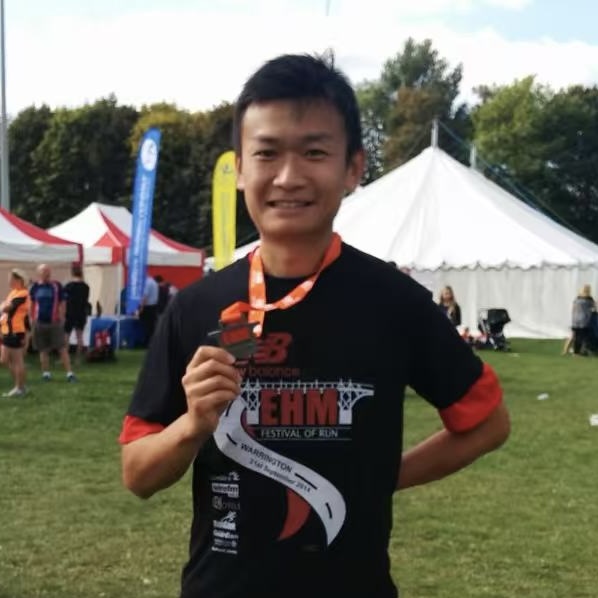
"Hi, I’m Dr Max Cao, I’m passionate about using AI and digital technologies to make industrial operations smarter, faster, and more sustainable. I love turning real-world challenges into practical solutions through innovation and collaboration. If you're interested in AI, digital twins, or industrial transformation, feel free to connect — I’d love to hear from you!"
Choose Golden Data
To better understand, manage, and unlock the value behind data, Golden Data firmly believes that the forthcoming era of data and intelligence will revolutionize the traditional manufacturing industry's production methods and operational models.
Empower through Data
Data becomes an asset of a company whose value appreciates through not only data accumulation but data usage, and the new insights and value created for stakeholders of an organization in optimizing operation.
Work with Experts
Golden Data has a professional team, composed of experienced data experts from renowned universities. The experts team uses a wide range of methods in research and gives advice on data processing and modelling.
Rely on Tenacity
We love the thing we are doing and confident on our solutions. The team tries to eliminate distractions and obstacles in the face of adversity in each project.
Interested in our work?
Turning Data into Value