Predictive Maintenance Powered by "Data-Driven + Digital Twin": Building an Intelligent Closed-Loop of Monitoring, Analysis, Prediction, Decision, and Feedback
1. Introduction to Digital Twin Technology
Digital twin technology creates virtual replicas of physical assets, enabling real-time monitoring, simulation, and optimisation. These digital counterparts are powered by IoT, big data, cloud computing, and AI, allowing them to continuously ingest and reflect operational data. From visualising performance in real time to simulating various operational scenarios, digital twins help industries reduce risks, cut costs, and enhance decision-making. They are now widely adopted in manufacturing, energy, aerospace, and smart cities, becoming a cornerstone of digital transformation.
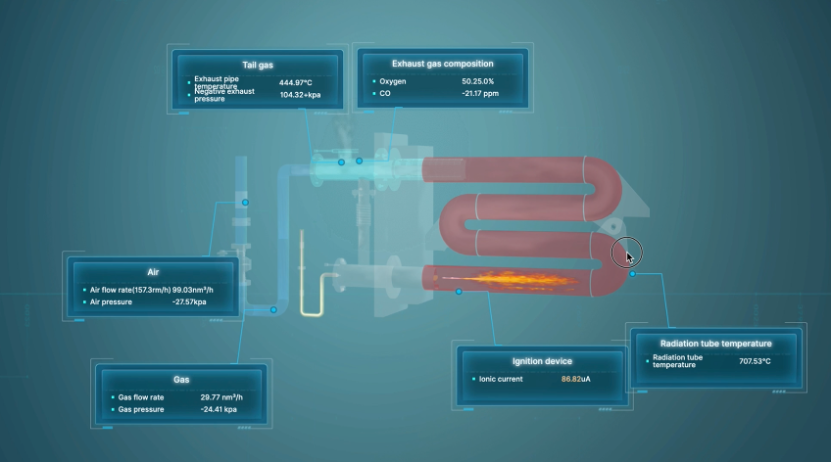
2. Industry Context and Market Demand
2.1 Industry Challenges
In today’s fast-paced manufacturing landscape, stable equipment operation is essential to ensure efficiency and profitability. Traditional maintenance approaches—whether reactive or scheduled—fall short. Reactive maintenance often leads to unexpected downtime and costly interruptions, while scheduled maintenance may result in over-servicing or missed failures due to fixed intervals.
Digital twin technology enables predictive maintenance by allowing equipment to be monitored in real time and potential faults to be identified before they occur. As sensors collect parameters like vibration, temperature, and pressure, digital twins process and analyse this data to spot deviations, compare current vs. ideal states, and trigger early warnings.
2.2 Industry Challenges
For large manufacturers, a single piece of faulty equipment can disrupt entire production lines. Predictive maintenance becomes a vital strategy for mitigating risks, reducing costs, and improving uptime. Meanwhile, SMEs—operating with tighter resources—seek the same capabilities for greater competitiveness. Regulatory pressures and growing safety expectations further increase the need for intelligent, reliable maintenance systems.
3. Pain Points in Traditional Maintenance
- Low Predictability: Traditional inspections are manual, infrequent, and subjective, making it difficult to predict faults accurately.
- High Maintenance Costs: Routine over-servicing wastes resources, while reactive maintenance leads to major disruptions and unplanned expenses.
- Conflict Between Uptime and Maintenance: Equipment downtime for servicing often competes with tight production schedules.
- Lack of Intelligence: Many factories still operate on a “fix it when it breaks” model, missing opportunities for efficiency and foresight.
4. The DPlus Advantage: Empowering Predictive Maintenance with Data and Intelligence
DPlus, developed by Golden Data, is an industrial intelligence platform that serves as the digital foundation for predictive maintenance. DPlus unifies data collection, processing, modelling, and AI-driven decision-making into one integrated solution.
It powers a closed-loop intelligence cycle:
“Monitoring → Analysis → Prediction → Decision → Feedback.”
Core Technical Highlights of DPlus:
- Data Acquisition: Real-time collection of multi-dimensional operational data via industrial-grade sensors.
- High-Fidelity Analytics: Utilises advanced AI/ML algorithms like LSTM, CNN, and Isolation Forest to predict failures and remaining useful life.
- Digital Twin Modelling: Combines physical structures, process logic, and behavioural simulation into dynamic digital replicas.
- Edge & Cloud Architecture: Supports flexible deployment, with edge pre-processing and seamless cloud integration.
- FMEA Integration: Automatically accumulates fault cases and solutions, forming an expert knowledge base for smart fault diagnosis and rapid response.
5. Application: Cold Rolling Mill Motor Monitoring
At a steel plant equipped with four ESP production lines and over 400 monitoring points, DPlus enabled real-time vibration and temperature monitoring across 63 critical machines. When the system detected abnormal vibration from the #1 R1 gearbox, it automatically triggered alerts, assisted in root cause analysis, and confirmed gear surface wear as the fault source. After timely maintenance, DPlus validated recovery through post-repair data, demonstrating its capability to close the loop from alert to resolution.
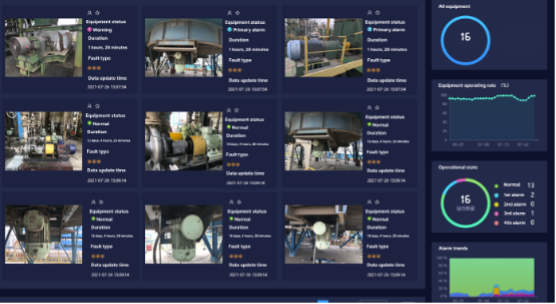
Moreover, the incident was logged in DPlus’ integrated FMEA library, making it instantly retrievable if similar patterns arise in the future. This speeds up future diagnostics and minimises downtime risks.
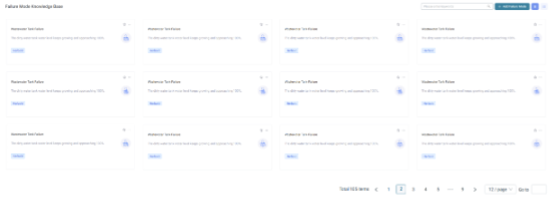
6. Value Delivered
- Enhanced Reliability: Digital twins powered by DPlus provide real-time fault detection and lifecycle prediction, reducing unexpected downtime.
- Reduced Costs: Maintenance is performed based on actual equipment condition—eliminating over-servicing and avoiding failure-induced losses.
- Smarter Decisions: Through advanced data analysis, DPlus supports data-driven strategies for equipment investment, replacement, and optimisation.
- Digital Knowledge Accumulation: DPlus builds a centralised, evolving knowledge base from real cases, supporting automation and continuous improvement.
Conclusion
DPlus is not just a digital platform—it’s a catalyst for transforming equipment maintenance from reactive to predictive, from fragmented to integrated, and from human-reliant to intelligent. By connecting data with action, and simulation with reality, DPlus empowers manufacturers to unlock the full potential of digital twins and data-driven maintenance.
Empower your operations with DPlus. Turn your data into real value.
For more information or to schedule a demo, contact us at: 📧 contact@goldendata.co.uk
About the Author
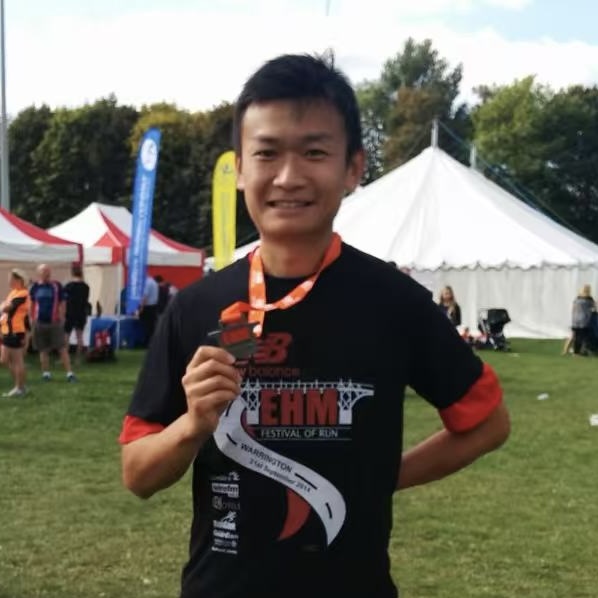
"Hi, I’m Dr Max Cao, I’m passionate about using AI and digital technologies to make industrial operations smarter, faster, and more sustainable. I love turning real-world challenges into practical solutions through innovation and collaboration. If you're interested in AI, digital twins, or industrial transformation, feel free to connect — I’d love to hear from you!"
Choose Golden Data
To better understand, manage, and unlock the value behind data, Golden Data firmly believes that the forthcoming era of data and intelligence will revolutionize the traditional manufacturing industry's production methods and operational models.
Empower through Data
Data becomes an asset of a company whose value appreciates through not only data accumulation but data usage, and the new insights and value created for stakeholders of an organization in optimizing operation.
Work with Experts
Golden Data has a professional team, composed of experienced data experts from renowned universities. The experts team uses a wide range of methods in research and gives advice on data processing and modelling.
Rely on Tenacity
We love the thing we are doing and confident on our solutions. The team tries to eliminate distractions and obstacles in the face of adversity in each project.
Further Exploration of The Digital Twin
Turning Data into Value